Table of Contents
- Introduction
- Types of Nondestructive Testing (NDT)
- Factors Influencing NDT Equipment Selection
- Key Features to Consider
- Future Trends in NDT Equipment
- Conclusion
- FAQs
Introduction
Ever wondered how critical it is for industries to make sure their products and infrastructure are rock-solid? Whether you’re a seasoned pro, a curious Non-Destructive Testing (NDT) enthusiast, or just someone intrigued by how things work, we’ve got all the answers and more. This guide will walk you through the rigorous testing processes with NDT equipment, quality control measures, and industry standards that ensure top-notch durability and reliability in products. You’ll gain valuable insights into the meticulous procedures of the NDT methods that go into creating products that stand the test of time.
NDT Products has been providing top-notch NDT equipment since 1977. Their range of products includes AGFA, Waygate Technologies, Circle Systems, Inc., Sherwin Incorporated, Echo Ultrasonics, Envirosight, Hitachi High Tech, Spectro-UV, REL Inc., Golden Engineering, Gould-Bass, Parker Research Corp., Ray-Check, and others.
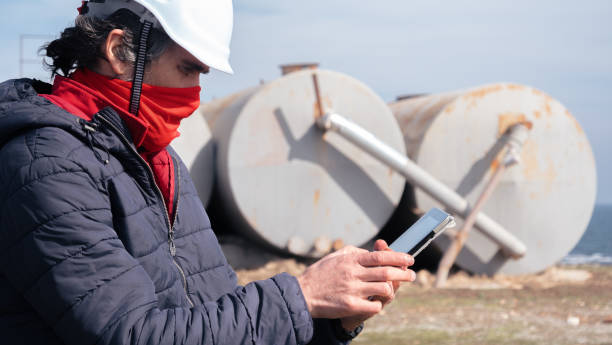
Types of NDT
NDT comprises a spectrum of methods, like ultrasonic examination, radiographic inspection, magnetic particle examination, and others. Every method necessitates bespoke products suited to its particular use, with diverse specifications for sensitivity, resolution, and reliability testing. Here are the various non destructive test methods.
1. Ultrasonic Testing
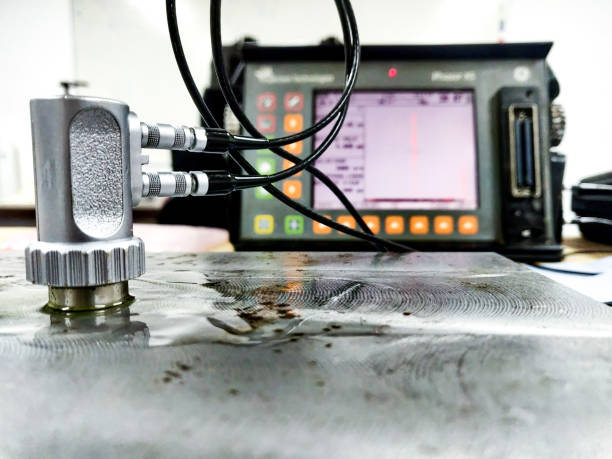
Ultrasonic Testing (UT) is a non-destructive testing (NDT) method employed to assess the integrity of materials by utilizing high-frequency sound waves. In this technique, a transducer generates ultrasonic waves that travel through the material being tested. When these waves encounter a boundary between different materials or a discontinuity within the material, such as a crack or void, they are reflected back to the transducer.
By analyzing the time taken for the echoes to return and their amplitude, technicians can determine the size, location, and characteristics of any defects present. Ultrasonic testing is widely used in various industries to detect flaws in welds, castings, and other structures, providing valuable information about the material’s structural integrity.
2. Radiographic Testing
Radiographic Testing (RT) involves the use of X-rays or gamma rays to inspect the internal structure of materials and identify potential defects. In this method, a radiation source is positioned on one side of the material, and a film or a digital detector is placed on the opposite side. The radiation penetrates the material, and variations in thickness, density, or the presence of defects result in differing levels of exposure on the film or detector.
This produces a radiographic image that allows technicians to detect flaws such as cracks, voids, or inclusions within the material. Radiography is commonly employed in assessing the integrity of welds in pipelines, pressure vessels, and other critical structures, providing detailed information about the internal quality of the inspected components.
3. Magnetic Particle Testing
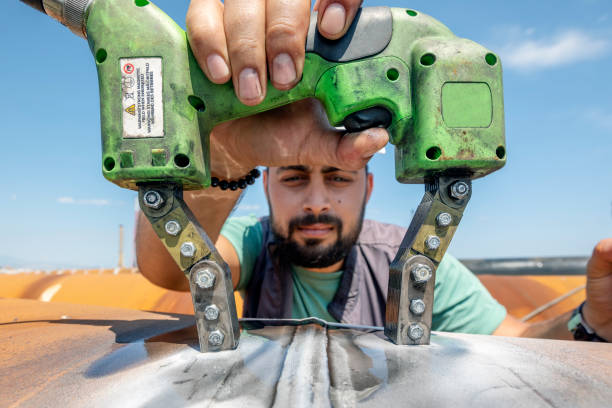
Magnetic Particle Testing (MPT) is a non-destructive testing method used to identify surface and near-surface defects in ferromagnetic materials such as iron and steel. In this technique, a magnetic field is applied to the material, and a magnetic particle (usually iron filings or a ferrous powder mixed with a liquid suspension) is applied to the surface. When a magnetic field encounters a discontinuity, such as a crack or flaw, the magnetic particles are attracted to and accumulate around the defect, forming visible indications.
These indications can be easily seen, allowing technicians to identify and evaluate the size, shape, and location of the defects. Magnetic particle testing is widely used in industries such as manufacturing, construction, and aerospace for the inspection of welds, castings, and other components.
4. Eddy Current Testing
When alternating current flows through a coil or probe, it creates electromagnetic currents in conductive materials. Eddy Current Testing (ECT) is a non-destructive way to test the integrity of these materials. Variations in the material, such as cracks, voids, or changes in thickness, have an impact on the magnetic field that results from the interaction between the induced eddy currents and the material’s electrical conductivity.
By measuring these changes, technicians can identify and characterise defects without direct contact with the material. Eddy current testing is particularly effective for inspecting non-ferrous metals and is widely applied in industries like aerospace, automotive, and electrical manufacturing for detecting surface and subsurface flaws in components like tubes, pipes, and conductive coatings.
5. Liquid Penetrant Testing
Liquid penetrant testing (LPT) is a non-destructive testing method used to detect surface defects in materials such as metals, plastics, and ceramics. In this technique, a liquid penetrant with high capillary action is applied to the surface of the material, allowing it to seep into any surface cracks or discontinuities.
After a specified penetration time, excess penetrant is removed, and a developer is applied to draw the trapped penetrant out of the flaws, making them visible. This method is particularly effective for identifying small cracks, porosity, and other surface irregularities, providing valuable insights into the integrity of the tested materials.
6. Visual Testing
Visual Testing (VT) is the simplest form of NDT, involving direct visual inspection of components or structures for any visible signs of damage, corrosion, or wear. While it may not detect internal defects, it is valuable for identifying surface abnormalities. Remote Visual inspection is the use of a camera or video borescope to visually inspect areas that would otherwise be impossible to access. For example, an on-wing aircraft engine.
Factors Influencing NDT Equipment Selection
Numerous factors exert considerable influence in selecting the optimal NDT equipment for a specific application. These include the properties of the material and components under scrutiny, industry-specific prerequisites like safety protocols and statutory provisions, and environmental elements.
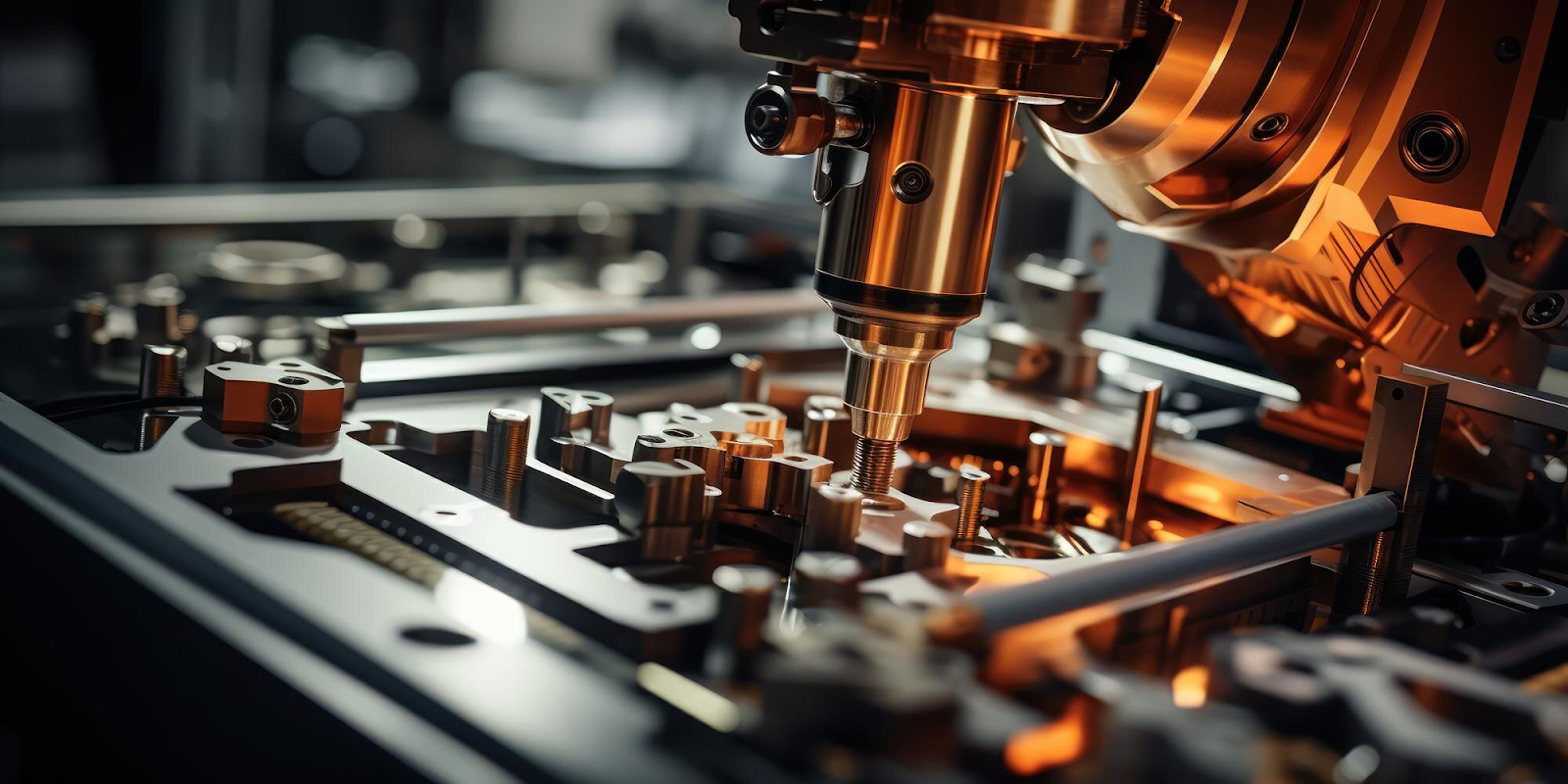
These factors range from the properties of the material and components under inspection to industry-specific standards and environmental conditions.
1. Material Characteristics: The type of material being tested greatly influences the choice of non destructive equipment. Different techniques are suited for various materials, such as metals, composites, plastics, or ceramics. For instance, ultrasonic testing is ideal for metals, while radiographic testing may be more suitable for composite materials.
2. Component Complexity: The complexity of the components being inspected also impacts equipment selection. NDT methods must be capable of detecting flaws or defects in intricate geometries, thin-walled structures, or components with varying thicknesses.
3. Industry Standards and Regulations: Compliance with industry-specific standards and regulations is paramount. NDT equipment selection must meet the requirements set forth by regulatory bodies and industry associations to ensure accurate and reliable inspections. This includes certifications and calibration procedures to maintain equipment integrity and performance.
4. Environmental Conditions: Environmental factors such as temperature, humidity, and ambient noise levels can affect the effectiveness of NDT inspections. Equipment must be robust enough to withstand harsh conditions encountered in various work environments, whether it’s in a factory, offshore facility, or remote field location.
5. Portability and Accessibility: Depending on the application, the portability and accessibility of NDT equipment may be crucial. In situations where inspections need to be conducted in confined spaces or remote locations, lightweight and portable devices are preferred. Additionally, equipment ergonomics and user-friendly interfaces enhance efficiency and ease of use.
Key Features to Consider
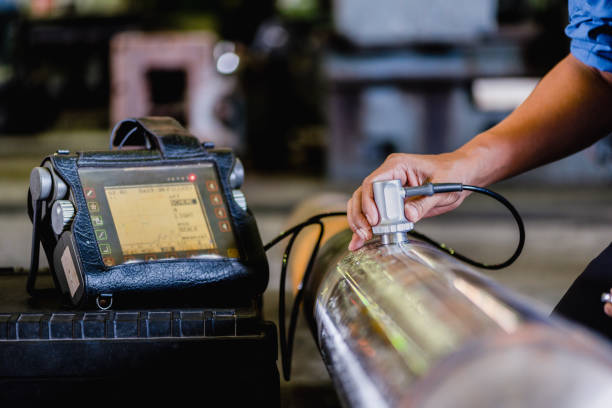
Choosing the right non destructive testing equipment involves evaluating several key features to ensure accurate, efficient, and reliable testing operations. These features encompass various aspects of equipment performance, usability, and maintenance requirements.
1. Sensitivity and Resolution: Imagine NDT equipment as sleuths with a knack for uncovering the tiniest secrets hidden within materials. Sensitivity is their superpower, allowing them to spot minuscule flaws that are invisible to the naked eye. Meanwhile, resolution is their clarity cloak, ensuring that every detail is crystal clear, like a high-definition movie revealing the intricacies of the plot.
2. Ease of Use: User-friendly interfaces and intuitive controls are essential for ensuring ease of operation, especially for technicians with varying levels of experience. Equipment with simple navigation menus, ergonomic design, and clear instructions minimizes the learning curve and facilitates efficient testing procedures.
3. Portability: The portability of NDT equipment is crucial, particularly for on-site inspections or fieldwork in remote locations. Lightweight, compact devices that are easy to transport and set up enable flexibility and accessibility in various testing environments. Portable equipment also enhances productivity by eliminating the need for cumbersome setups or specialized.
5. Calibration and Maintenance Requirements: Regular calibration and maintenance are essential to ensuring the accuracy and reliability of NDT equipment over time. Choosing equipment with straightforward calibration procedures and minimal maintenance requirements simplifies upkeep tasks and reduces downtime. Additionally, access to reliable technical support and servicing options is vital for addressing any issues promptly and maintaining optimal performance.
6. Compatibility and Integration: NDT equipment selection should be compatible with existing systems and software platforms to facilitate seamless integration into the testing workflow. Interoperability with data management software, analysis tools, and reporting systems streamlines data processing and enhances productivity. Furthermore, the ability to integrate with emerging technologies such as cloud-based solutions and wireless connectivity can future-proof NDT operations and support evolving industry trends.
7. Safety Features: Last but certainly not least, safety is our guiding star in the NDT world. With built-in safety features like radiation shielding and temperature monitoring, our heroes are equipped to handle any challenge while keeping our technicians out of harm’s way. It’s not just about following the rules.
By carefully evaluating these key features, organizations can make informed decisions when selecting NDT equipment that aligns with their specific testing requirements, operational needs, and quality assurance objectives.
Future Trends in NDT Equipment
Technological advancements and shifting industry demands are driving constant change in the field of NDT. Emerging trends include the integration of artificial intelligence and machine learning for data analysis, the development of portable and wireless NDT solutions, and the adoption of advanced imaging techniques for enhanced defect detection.
As technology continues to advance and industry requirements evolve, the field of non destructive testing is witnessing several notable trends shaping the future of NDT. These trends encompass innovative approaches to data analysis, the design of portable and wireless solutions, and the integration of advanced imaging techniques to improve defect detection capabilities.
1. Integration of Artificial Intelligence and Machine Learning: Artificial intelligence (AI) and machine learning (ML) technologies are revolutionizing NDT by enhancing data analysis capabilities and automating decision-making processes. AI algorithms can interpret vast amounts of inspection data rapidly, identify patterns, and predict potential defects with greater accuracy. Machine learning algorithms can also adapt and improve over time, leading to more efficient and reliable inspection outcomes.
2. Development of Portable and Wireless Solutions: The demand for flexible, on-the-go NDT solutions is driving the development of portable and wireless equipment. Portable devices offer increased mobility and accessibility, allowing inspections to be conducted in remote or challenging environments where traditional equipment may be impractical. Wireless connectivity enables real-time data transmission, remote monitoring, and seamless integration with digital platforms, enhancing productivity and efficiency in NDT operations.
3. Adoption of Advanced Imaging Techniques: Advanced imaging techniques, such as computed tomography (CT), phased array ultrasonics (PAUT), and digital radiography (DR), are being increasingly utilized in NDT for enhanced defect detection and characterization. These techniques provide detailed, three-dimensional images of internal structures, enabling more accurate assessments of complex components and materials. Furthermore, advancements in sensor technology and image processing algorithms are driving improvements in image quality, resolution, and reconstruction speed, further enhancing the capabilities of these imaging modalities.
4. Innovations in Sensor Technology: The development of innovative sensor technologies is expanding the capabilities of NDT equipment, enabling more sensitive and versatile inspections. Emerging sensor technologies, such as laser-based measurement systems, terahertz imaging, and electromagnetic sensors, offer unique advantages for detecting and characterizing defects in a wide range of materials and environments. These sensors can provide valuable insights into material properties, surface conditions, and structural integrity, enhancing the effectiveness of NDT inspections.
5. Integration of Augmented Reality (AR) and Virtual Reality (VR): Augmented reality (AR) and virtual reality (VR) technologies are being integrated into NDT equipment to enhance visualization, training, and collaboration capabilities. AR overlays digital information onto the real-world environment, providing technicians with contextual guidance and visual aids during inspections. VR simulations enable immersive training experiences, allowing technicians to practice NDT techniques in virtual environments before conducting actual inspections. These technologies improve efficiency, accuracy, and safety in NDT operations while reducing training costs and downtime.
By embracing these future trends and leveraging innovative technologies, non destructive testing techniques are poised to achieve greater efficiency, accuracy, and reliability, ultimately enhancing safety, quality assurance, and asset integrity across various sectors.
Conclusion
Selecting the right NDT equipment is paramount for ensuring the quality and safety of products and infrastructure across various industries. By understanding the types of nondestructive testing techniques, equipment requirements, and key factors influencing selection, businesses can make informed decisions to meet their testing needs effectively. Stay updated on future trends to leverage the latest advancements in NDT technology for improved inspection capabilities and enhanced quality assurance.
FAQ
Non-Destructive Testing (NDT) employs a variety of equipment, depending on the method being used. Commonly used equipment includes ultrasonic testing machines, radiographic equipment (X-ray and gamma-ray), eddy current testing instruments, magnetic particle testing equipment, dye penetrant inspection kits, visual inspection tools, and thermographic cameras.
While there are numerous NDT techniques, the six most common testing methods include:
a. Ultrasonic Testing (UT)
b. Radiographic Testing (RT)
c. Magnetic Particle Testing (MPT)
d. Dye Penetrant Testing (PT)
e. Visual Testing (VT)
F. Eddy Current (EC)