Need for Lithium-ion Battery Inspection Solutions
Demand for batteries is steadily growing and with it the demands on even faster development cycles combined with product safety and quality. Highly flexible and accurate testing and inspection of prototype batteries as well as the full scale production of batteries with industrial X-ray CT solutions is required.
Key stakeholders in the battery industry require detailed product cell/module/pack visibility in different stages of the product life cycle:
- Electrode/cell/module development – prototype analytics, verification of design changes, before/after test comparison, assembly quality control
- Production quality – statistical product quality control in manufacturing process, verification of design, product and process changes
- Testing of used, damaged and/or refurbished batteries for failure analysis
- Optical or X-ray navigation map for overview of large size samples and fast positioning
Battery Manufacturing – Where and How CT can Add Value (Graphic)
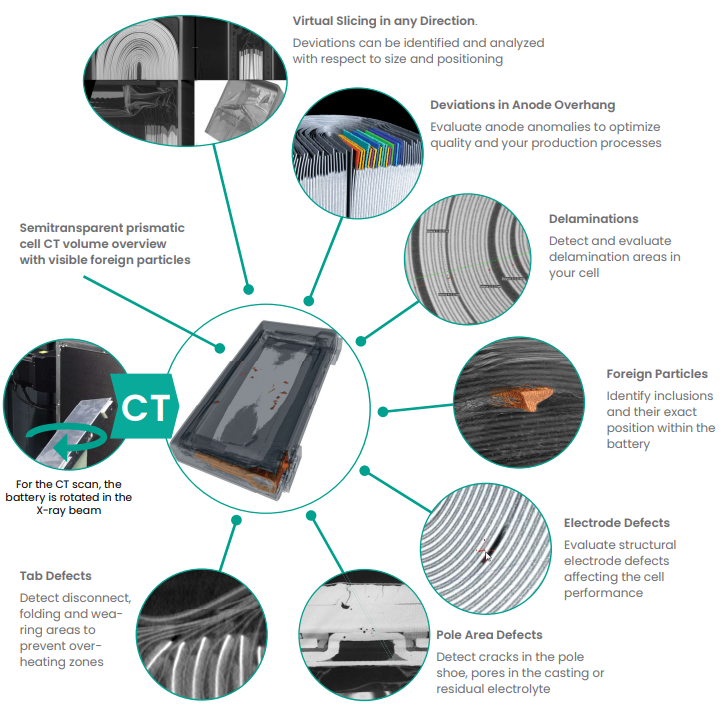
Phoenix CT for Battery Inspection – Your Advantages
- Non-destructive and 3D analysis – faster and more accurate results compared to conventional destructive laboratory methods reaction times
- Allows to visualize and analyze structure and geometry in 3D with one scan
- Adaptable solutions for existing and new battery and manufacturing technologies
- Adaptable solutions from OEM to different battery cell & module sizes
- In lab and on production floor – even in same production line
- Holistic digital data about production quality for fast process optimization and significant shorter ramp-up times
- Future-proof inspection technology applicable for all actual kinds auf Li-ion, but also future solid-state battery types
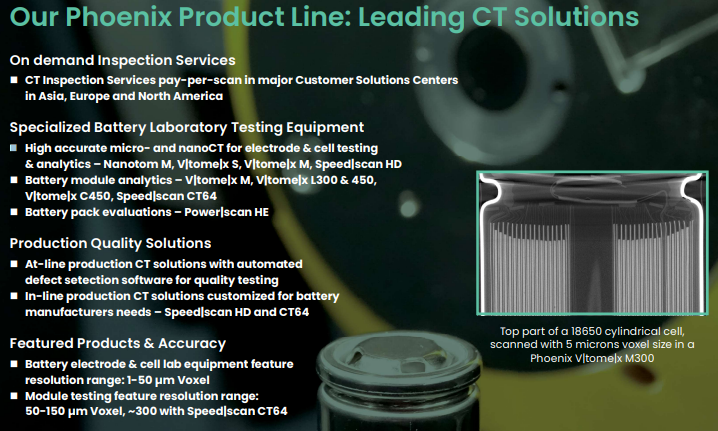
With Computed Tomography Solutions from Waygate Technologies, NDT Products Limited is proud to offer a cutting-edge solution that embodies innovation, reliability and standards.
Explore our ndt for batteries solutions from our partner: waygate technologies