Table of Content
- How Eddy Current Testing Works?
- Types of Eddy Current Testing Probes
- Factors Influencing Probe Selection
- Eddy Current Testing Equipment
- Applications of Eddy Current Probes
- Eddy Current Testing Techniques
- Advantages of Eddy Current Testing
- Conclusion
Eddy current testing probes are widely used in non-destructive testing processes. Whether you’re in aerospace, automotive, or power generation, understanding ECT and its probes is vital for effective defect detection and quality control. Eddy current testing for defect detection plays a crucial role in various industries, ensuring the integrity and safety of critical components.
How Eddy Current Testing Works?
Eddy Current Testing leverages electromagnetic induction to identify defects without damaging the material. ECT operates on the principle of electromagnetic induction. When an alternating current passes through a coil, it generates an alternating magnetic field.
This magnetic field induces eddy currents in the conductive material under inspection. Disruptions in the flow of these eddy currents indicate the presence of flaws.
Types of Eddy Current Testing Probes

Selecting the right probe is crucial for accurate eddy current testing results. Probes come in various types, each suited for specific applications. Here’s an overview of the eddy current probe types and their uses.
1. Surface Probes
Surface probes are designed for detecting flaws on or near the surface of a material. They are commonly used in applications where only the surface layer needs to be inspected. These probes are highly sensitive to surface irregularities, making them ideal for detecting cracks and corrosion.
Advantages
- High sensitivity to surface defects.
- Suitable for inspecting complex geometries.
Limitations
- Limited penetration depth, making them ineffective for detecting deeper flaws.
2. Encircling Probes
Encircling probes, also known as circumferential probes, are used for inspecting cylindrical objects such as pipes and rods. These probes encircle the test object, providing 360-degree coverage.
Advantages
- Complete inspection coverage.
- Ideal for uniform cylindrical objects.
Limitations
- Limited to cylindrical shapes.
- Potentially cumbersome for large objects.
3. Internal Probes
Internal probes are designed to inspect the inner surfaces of hollow structures. They are commonly used for applications like inspecting the inside of tubes and boreholes.
Advantages
- Effective for internal surface inspection.
- Can access hard-to-reach areas.
Limitations
- Limited to hollow objects.
- May require specialized equipment for positioning.
Factors Influencing Probe Selection
Factors influencing probe selection include the material being tested, the surface condition, and the desired sensitivity of the inspection. Choosing the right probe depends on several factors, including:
- Material Type and Thickness
Different materials respond differently to eddy currents. Probes must be compatible with the material’s
- Conductivity and thickness.
Surface Condition and Accessibility
The probe must be able to navigate the surface conditions and reach the area of interest effectively.
Eddy Current Testing Equipment
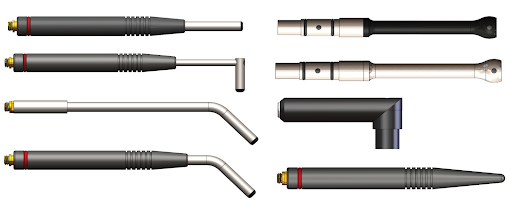
Eddy current testing equipment consists of several key components, including a probe or coil, a signal generator, and a display unit. The probe, typically made of a conductive material, is used to induce eddy currents in the test material and detect any changes in conductivity.
1. Probe
The main tool for inducing and detecting eddy currents is essential for accurately identifying defects or inconsistencies in the material being tested.
2. Instrument
The device that powers the probe and processes the signals received from the probe is known as the signal generator.
3. Display Unit
A visual representation of the detected flaws allows for easy interpretation of the data collected during the testing process.
4. Software
For data analysis and reporting , specialized software is often used in conjunction with the eddy current testing system.
NDT Products, Waygate Technologies Eddy Current Probe Accessories are available throughout Canada.They are fast, accurate, and cost-effective method for detecting surface and near-surface flaws in raw materials, finished products, and maintenance inspections.
NDT Products offers Aerofab NDT Eddy Current Probes, reference standards, and accessories in Canada, providing high-quality testing tools for the aerospace and aviation industries, with over 50 years of experience.
Applications of Eddy Current Probes
Eddy Current Probes are used in various industries for different purposes. These probes are commonly used in various industries for detecting surface cracks in engine parts.
- Aerospace
Inspecting aircraft components for cracks and corrosion is a common application of eddy current probes in the aerospace industry. Additionally, these probes are also utilized for measuring material thickness and conductivity in non-destructive testing processes.
- Automotive
Checking engine parts and other critical components for cracks, wear, and defects is another important application of eddy current probes in the Automotive Industry. These probes can also be used for quality control during manufacturing processes to ensure the integrity of the final product.
- Power Generation
Inspecting turbines and other equipment for cracks, erosion, and other defects is a crucial use of eddy current probes in the power generation industry. Furthermore, these probes can help monitor the condition of heat exchangers and piping systems to prevent potential failures.
- Manufacturing
Quality control in production lines can be enhanced with the use of eddy current probes to detect surface defects and ensure product reliability. Additionally, these probes can assist in monitoring the integrity of welds and detecting flaws in materials during the manufacturing process.
Eddy Current Testing Techniques
Eddy current testing techniques utilize various types of probes to detect surface and near-surface defects in conductive materials. Some common probes include absolute, differential, and rotating probes, each offering unique advantages for different testing applications. There are several techniques within ECT, each suited for different applications:
- Single-Frequency Testing
Simple and widely used for basic inspections.
- Multi-Frequency Testing
Uses multiple frequencies to detect a wider range of defects.
- Pulsed Eddy Current Testing
Suitable for inspecting thick or layered materials.
Advantages of Eddy Current Testing

Eddy current testing utilizes various types of probes, including absolute, differential, and encircling probes. These probes offer advantages such as non-contact inspection, high sensitivity to surface cracks, and the ability to detect conductivity changes in materials.
1. Non-Destructive
ECT does not harm the material being tested and can be used on a wide range of conductive materials, making it a versatile inspection method for industries such as aerospace, automotive, and manufacturing. Additionally, ECT can provide fast and accurate results, allowing for efficient quality control processes.
2. High Sensitivity and Accuracy
Capable of detecting very small defects that may not be visible to the naked eye, eddy current testing is a valuable tool for ensuring the integrity of critical components. Its ability to provide precise and reliable results makes it an essential technique for industries where safety and quality are top priorities.
3. Versatile
It can be used on a wide range of materials and shapes , including conductive materials like metals and non-conductive materials like composites. This versatility makes eddy current testing a practical choice for various industries looking to ensure the quality of their products.
Conclusion
Eddy current testing is a powerful tool for ensuring the integrity of critical components across various industries. By understanding the different types of probes and their applications, technicians can effectively detect and address flaws, ensuring safety and quality.
At NDT Products, we focus on precision. Our mission is to provide you with the tools you need to ensure safety, efficiency, and peace of mind. Join the countless satisfied clients who trust us to deliver excellence in every test.
We offer a wide range of high-quality probes specifically designed for eddy current testing, allowing you to choose the best option for your specific needs. Trust NDT Products to provide you with reliable and accurate results every time.