SPP Pumps was founded in 1875 by a British engineer after he bought the patent rights of the Pulsometer Pump from the American Thomas Hall. For more than 100 years SPP Pumps has been a leading manufacturer of centrifugal pumps and
systems, providing high integrity services for diverse industries such as oil and gas production, airports, hotels, water and waste water treatment, construction, mines and large industrial plants. With a manufacturing facility in Coleford, UK, and multiple locations worldwide for sales, manufacturing, and service, SPP Pumps sets the highest standards attainable in the industry for quality and reliability.
” The X-MET8000 helps us improve our product quality throughout our process. Checking material on the shop floor before it is used in production gives us extra confidence. ”
THE NEED FOR TESTING
SPP Pumps knows that product failure could have potentially catastrophic consequences. The company’s Quality Assurance department decided to investigate how the use of Hitachi High-Tech’s handheld X-ray fluorescence (XRF) analyser, the X MET8000, could help improve product quality throughout its manufacturing process, whilst saving costs on third party testing.
Andrew Warren, Quality Inspector at SPP Pumps carried out testing of a wide variety of materials (stainless steel, brass, superduplex alloys, etc.) in four main areas: incoming inspection of parts, material verification on the shop floor, final acceptance testing, and testing during repair or maintenance.
INCOMING INSPECTION: “TRUST BUT VERIFY”
It’s crucial that parts used for the manufacture of safety-critical equipment meet stringent specifications. The X-MET can be used to verify alloy grade and chemistry on 100% of parts being delivered and results can be compared to the vendors’ certificates. If certificates are missing, the parts would normally be quarantined until their paperwork arrives. This is no longer the case as the X-MET enables on-the-spot verification, allowing the parts to move directly to stock, thus minimizing manufacturing delays. Results can be sent to a portable Bluetooth printer, and the small printout or label can be attached to the tested part for future reference, minimizing any potential mix-ups down the line.
MATERIAL VERIFICATION ON THE SHOP FLOOR
Similar-looking alloys are likely to have different physical and mechanical properties. It’s often impossible to differentiate them by visual inspection. With the X-MET, users can check materials before picking them up from the racks or shelves and moving them into the production process. This simple and quick step removes the risk of using the wrong component and optimises quality assurance.
FINAL ACCEPTANCE TEST
Once a pump has gone through its manufacturing process and final internal tests, an external inspector is contracted by the end-user to witness final acceptance activities. This involves checking that all required paperwork is present and correct, and that the pump performs as expected. If a single
material certificate is missing, payment and shipment could be put on hold until the certificate is provided, impacting on SPP’s revenue for the month. There again, the X-MET can provide the missing information for any material lacking paperwork, enabling the FAT testing to continue and be completed on the day, and the pump to be invoiced fully.
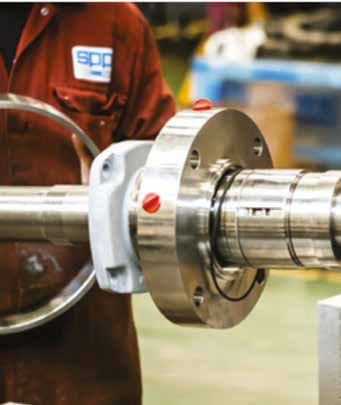
TESTING DURING REPAIR OR MAINTENANCE AT SERVICE CENTRES
To ensure long-term quality and reliability of the pumping machinery they manufacture, SPP also carry out service at various locations worldwide. There, the X-MET8000 Expert helps confirm that all components of the serviced pump are genuine (i.e. have not been replaced/repaired by a third party), and it can also be used to verify that the correct material is used for the replacement parts, ensuring the product quality is maintained throughout its life.
HOW THE X-MET HELPS INCREASE AND MAINTAIN PRODUCT QUALITY.
Andrews said: “The X-MET8000 helps us improve our product quality throughout our process. We can check material and confirm chemical analysis during incoming inspection, so parts can be stored and moved into production quicker, or they can be rejected on the spot if they do not match the expected specification. We can also compare results with the suppliers’ certificates and confirm material to internal or external inspectors. Checking material on the shop floor before it is used in production also gives us extra confidence that the equipment we build will meet our and our customers’ high standards”.