Table of Content
- Basic Principles of Liquid Penetrant Testing
- Types of Liquid Penetrant Testing
- Liquid Penetrant Testing Process
- Liquid Penetrant Testing Equipment
- Liquid Penetrant Testing Materials
- Benefits of Liquid Penetrant Testing
- Applications of Liquid Penetrant Testing
- Conclusion
Non-destructive testing is a crucial part of many industries. It ensures the safety and integrity of materials and components without causing damage. One common and accessible NDT method is Liquid Penetrant Testing. But what is liquid penetrant examination, and why is it important?
Basic Principles of Liquid Penetrant Testing
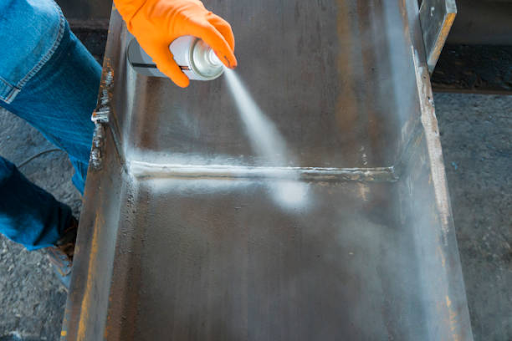
Liquid penetrant material Non-destructive Testing Method is used to detect surface-breaking defects in non-porous materials. The basic principle involves applying a liquid penetrant materials to the surface of the material being tested.
The penetrant seeps into any surface defects, such as cracks or porosities. After a specified dwell time, the excess penetrant is removed, and a developer is applied, drawing the penetrant out of the defects to form visible indications. This method is highly sensitive and can detect very small defects that may not be visible to the naked eye. A liquid penetrant testing kit is commonly used in industries such as Aerospace, automotive, and manufacturing to ensure the quality and integrity of components.
Types of Liquid Penetrant Testing
When you put a liquid penetrant on the surface of non-porous materials like metals, plastics, and ceramics, it finds flaws that go through the surface. This is called fluorescent and visible dye penetrant inspection. There are several types of liquid penetrant testing methods based on the type of penetrant and developer used.
Water-Washable Penetrants:
Water-washable penetrants are easily removed with water after the inspection process, making them environmentally friendly. These penetrants are commonly used in industries where cleanliness is a priority, such as aerospace and medical device manufacturing.
Post-Emulsifiable Penetrants:
Post-emulsifiable penetrants are designed to be removed with a solvent-based emulsifier after the inspection process. This type of penetrant is often used in situations where water-washable penetrants may not be suitable, such as in high-temperature applications.
Solvent-Removable Penetrants:
Solvent-removable penetrants are removed using a solvent cleaner, making them ideal for applications where water cannot be used. This type of penetrant is often preferred in industries like automotive and heavy machinery manufacturing.
Liquid Penetrant Testing Process
The liquid penetrant testing process is a non-destructive testing method used to detect surface-breaking defects in non-porous materials. This process involves applying a liquid penetrant to the surface of the material, allowing it to seep into any cracks or defects, and then removing the excess penetrant before applying a developer to highlight any indications. Which order is right for liquid penetrant test? The LPT process involves several steps.
- Pre-cleaning:
Removing dirt, grease, and other contaminants from the surface.
- Application of Penetrant
Applying the liquid penetrant to the surface.
- Dwell Time
Allowing the penetrant to seep into defects.
- Excess Penetrant Removal
Removing the excess penetrant from the surface.
- Application of Developer
Applying a developer to draw out the penetrant from defects.
- Inspection
Examining the surface under suitable lighting conditions to detect defects.
- Post-cleaning
Cleaning the tested surface to remove all testing materials.
LPT examination involves visually inspecting the surface under appropriate lighting. Fluorescent penetrants require UV light, while visible dye penetrants can be inspected under white light. The inspector looks for indications that suggest surface defects.
The developer draws these indications out, making them more obvious during the inspection process. Once the inspection is complete, the surface is thoroughly cleaned to remove any remaining testing materials.
Liquid Penetrant Testing Equipment
LPT is used to detect surface-breaking defects in non-porous materials such as metals, plastics, and ceramics. This method involves applying a liquid penetrant to the surface of the material, allowing it to seep into any cracks or flaws before being wiped away and covered with a developer to highlight any indications.
1. Penetrant Spray or Dip Tanks:
For applying the penetrant. These tanks can be manual or automated, depending on the size and complexity of the parts being tested. They ensure thorough coverage of the penetrant on the surface, maximizing the chances of detecting any defects present.
2. Emulsifiers and Solvents:
For removing excess penetrant. Emulsifiers are used to remove excess penetrant from the surface, while solvents are used to clean the surface before applying the penetrant. These chemicals help ensure accurate and reliable results in non-destructive testing processes.
3. Developer Applicators:
For applying the developer. Developer applicators are used to evenly apply the developer on the surface after the excess penetrant has been removed. This step helps to draw out any indications of defects that may be present, making them easier to detect during inspection.
4. UV Light (for fluorescent penetrants):
To enhance the visibility of indications. UV light is used specifically for fluorescent penetrants to make indications of defects more visible. This step is crucial in detecting any flaws that may be present on the surface being inspected.
5. Inspection Booths:
Controlled environments for conducting inspections. Inspection booths are equipped with proper lighting and ventilation to ensure accurate and thorough inspections can be carried out. These controlled environments help to minimize external factors that could affect the inspection process.
The LP1 by NDT Products is the first of three standard penetrant inspection systems. This LP1 is durable, user-friendly, and cost-effective, making it the new go-to system in the industry. It is designed for method A, B, and D liquid penetrant inspections, and is built in Canada. The system features a powder-coated steel frame, stainless steel stations, soft-close tank lids, a walk-in inspection station, and accessories like a UV-A light.
Liquid Penetrant Testing Materials
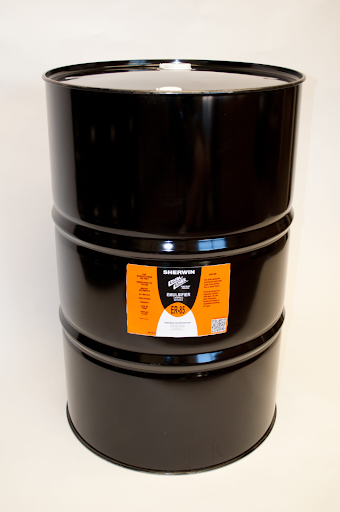
Liquid Penetrant Testing materials are used to detect surface-breaking defects in non-porous materials such as metals, plastics, and ceramics. What are the materials used in penetrant testing? The materials typically consist of a penetrant, developer, and cleaner to ensure accurate results.
1. Penetrants
Fluorescent or visible dye penetrants are typically brightly coloured to enhance visibility and can be either fluorescent or non-fluorescent, depending on the specific application requirements. Additionally, the developer is used to draw the penetrant out of the defects, making them more visible for inspection.
2. Emulsifiers
Emulsifiers are sometimes used in liquid penetrant testing to remove excess penetrant from the surface before applying the developer. This helps to prevent false indications and ensures accurate results during inspection.
3. Solvents
Solvents are used to clean the surface before applying the penetrant, ensuring that any contaminants or debris do not interfere with the inspection process. Additionally, solvents can be used to remove excess penetrant after the inspection is complete, leaving a clean surface for further analysis.
4. Developers
Developers are applied after the penetrant has been removed to draw out any remaining penetrant from discontinuities in the material, making them more visible for inspection. They work by creating a contrasting background that highlights any indications present on the surface.
The Sherwin ER-85 Emulsifier is a Method B emulsifier that is used to get rid of extra surface penetrant in inspection penetrant processes. It meets low sulphur, low halogen, and low-sodium requirements and offers low background visibility, long material tank life, and a clean, odourless product.
Sherwin ER-83C is a hydrophilic emulsifier used to emulsify non-water washable penetrants, effectively removing surface penetrants through spray or immersion.
Benefits of Liquid Penetrant Testing
Liquid Penetrant Testing is a cost-effective, simple, and sensitive method for detecting surface-breaking defects in various materials, offering ease of use and sensitivity to small discontinuities. There are many benefits to liquid penetrant testing.
1. High Sensitivity
LPT is highly sensitive to small surface defects, making it an invaluable tool for quality assurance.
2. Cost-Effectiveness
Compared to other NDT methods, LPT is relatively inexpensive, requiring minimal equipment and materials.
3. Versatility
LPT can be used on a variety of materials, including metals, ceramics, and plastics.
4. Simple Procedure
The testing process is straightforward and does not require extensive training.
5. Minimal Equipment Required
Basic LPT can be performed with just a penetrant, developer, and light source, making it accessible for many applications.
Applications of Liquid Penetrant Testing
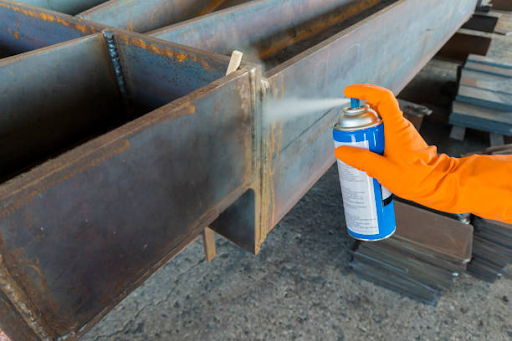
Applications of liquid penetrant testing include detecting cracks, porosity, leaks, and other surface defects in components such as welds, castings, and forgings. Additionally, LPT can be used in industries such as aerospace, automotive, and manufacturing to ensure the quality and integrity of parts.
1. Aerospace Industry
In the aerospace sector, LPT is used to inspect critical components such as turbine blades and landing gear for cracks and other defects.
2. Automotive Industry
LPT helps ensure the safety and reliability of automotive parts, including engine components and chassis.
3. Construction Industry
In construction, LPT is employed to check the integrity of welds and structural components.
4. Oil and Gas Industry
LPT is crucial in the oil and gas sector for inspecting pipelines, storage tanks, and drilling equipment.
5. Power Generation Industry
Power plants use LPT to inspect turbines, boilers, and pressure vessels to prevent failures and ensure efficiency.
Conclusion
Liquid penetrant testing is a handy and affordable way to find surface defects in many materials. Its ease and accuracy make it useful in many fields, from aerospace to construction. Knowing how LPT works helps professionals keep their parts and structures safe and sound. By understanding the process and limitations of liquid penetrant testing, professionals can effectively identify and address potential issues before they become major problems. This proactive approach can ultimately save time, money, and prevent accidents or failures in various industries.
NDT Products ensures safety by detecting potential issues before they become problems. We provide better technology, ultimately saving time and money in the long run. By investing in our products, you are investing in the safety and success of your operations.