Table of Contents
- Introduction
- Understanding Magnetic Particle Inspection
- Advantages of Magnetic Particle Inspection
- Applications of Magnetic Particle Inspection
- Best Practices in Magnetic Particle Inspection
- Conclusion
- Key Takeaways
- FAQs
Introduction
Magnetic Particle Inspection (MPI) can safeguard your industry’s critical components. Magnetic particle inspection stands as a cornerstone in various industries, offering a non-destructive testing method that’s both reliable and efficient. MPI testing detects hidden flaws open to the surface and even just beneath the surface, from tiny cracks to imperceptible inclusions.
Understanding Magnetic Particle Inspection
MT test procedure relies on the principles of magnetism and ferrous particles to identify surface and near-surface defects in materials. This subsection delves into the science behind MPI, explaining how the process works to pinpoint imperfections that may otherwise go unnoticed.
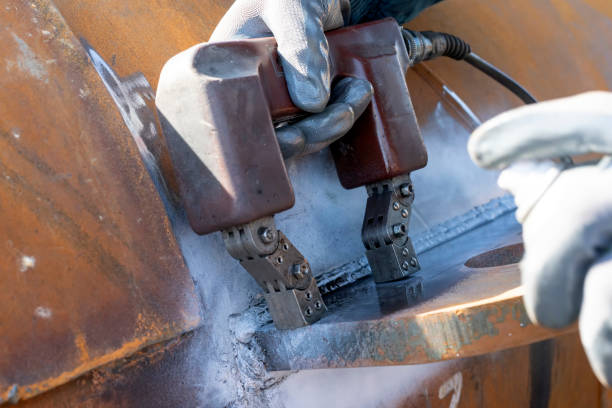
The principles of MPI inspections revolve around utilizing magnetism and ferrous particles to identify surface and near-surface defects in materials. This method capitalizes on the inherent magnetic properties of ferrous materials, such as iron and steel. Here are the steps.
1. Magnetization: The first step involves magnetizing the component under inspection. A yoke or coil-generated magnetic particle inspection test field can accomplish this. As the material becomes magnetized, any existing defects or irregularities will disturb the magnetic field.
2. Application of Magnetic Particles: Once magnetized, ferrous particles, often in the form of a dry powder or liquid suspension, are applied to the surface of the material. These particles are attracted to the areas where the magnetic field is distorted, highlighting potential defects.
3. Formation of Indications: The magnetic particle accumulates and forms visible indications at the locations of defects. These indications are typically characterized by their distinct patterns, making it possible to identify the nature and size of the flaws.
4. Inspection Process: The inspector examines the component under proper lighting conditions, looking for the indications created by the accumulated magnetic particles. The presence, size, and shape of these indications help determine the nature and extent of any defects in the material.
Advantages of Magnetic Particle Inspection
Magnetic particle inspection in non-destructive testing can be used on complex shapes and sizes of parts, making it a versatile inspection technique for a wide range of industries. Here are the advantages of magnetic particle inspection.
1. High Sensitivity and Speed: Magnetic penetrant inspection is highly sensitive to surface and near-surface defects, even those invisible to the naked eye. This exceptional sensitivity allows for the quick and reliable detection of flaws in materials. The speed of the inspection process is another notable advantage. Mag particle inspection can rapidly assess components, making it ideal for high-volume production environments where efficiency is paramount.
2. Cost-Effectiveness: Compared to some other non-destructive testing methods, magnetic tests prove to be a cost-effective solution. Its efficiency in detecting defects reduces the need for extensive and expensive follow-up inspections, contributing to overall cost savings.
3. Versatility in Applications: The magnetic inspection test finds widespread use across various industries, including aerospace, automotive, and manufacturing. Its versatility makes it suitable for inspecting a wide range of materials and components, enhancing its applicability.
4. Minimal Surface Preparation: MPI requires minimal surface preparation before inspection. This is advantageous, especially when dealing with complex geometries or components with irregular surfaces. The simplicity of the preparation process adds to the efficiency of MPI inspections.
5. Real-Time Results: The indications created during the MPI process are visible in real-time. This immediate feedback allows inspectors to promptly assess the condition of the material and make informed decisions about its suitability for use.
6. Localized Inspections: MPI can be applied to specific areas of a component, allowing for targeted inspections. This localized approach is beneficial in situations where only certain parts of a structure or material need assessment, optimizing the inspection process.
Applications of Magnetic Particle Inspection
Industry-Specific Applications
Aerospace: In the aerospace industry, where the structural integrity of components is paramount, magnetic particle inspection is extensively employed. From aircraft engines to critical structural elements, MPI ensures that potential defects such as cracks or fatigue do not compromise the safety and performance of aerospace materials.
Automotive: Automotive manufacturing relies on MPI for quality control in components like engine parts, axles, and critical welds. Detecting defects early in the production process helps prevent component failure and ensures the overall reliability of vehicles on the road.
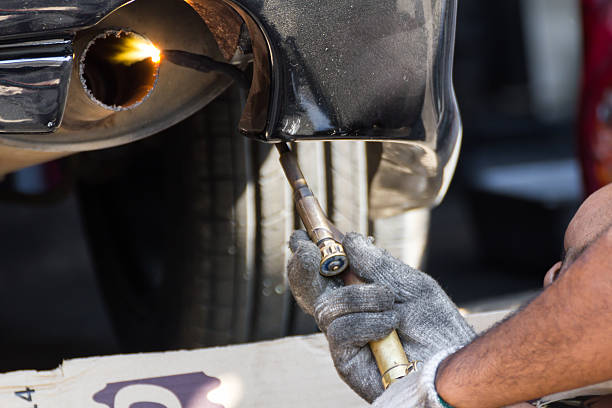
Manufacturing: In the broader manufacturing sector, MPI plays a crucial role in inspecting various materials and components, including welds, gears, and structural elements. The method’s ability to swiftly identify defects enhances the overall quality assurance process, contributing to the production of reliable and durable goods.
Oil & Gas Industry: The Oil & Gas industry often faces harsh environmental conditions, and components used in the oil & gas infrastructure must withstand extreme stress. MPI is employed to inspect critical components like pipelines, underwater pipelines, pressure vessels, etc. ensuring they are free from defects that could compromise their structural integrity in challenging environments.
Power Generation: In the power generation sector, particularly with the production of turbines and generators, MPI is crucial for inspecting components exposed to high temperatures and stress. This application helps prevent unexpected failures and ensures the continuous and safe operation of power generation facilities.
Rail Transportation: For the rail industry, the safety of rail components is paramount. Magnetic field testing is used to inspect train wheels, rails, and other critical parts for defects that could lead to catastrophic failures. This application contributes to the overall reliability and safety of rail transportation systems.
Best Practices in Magnetic Particle Inspection
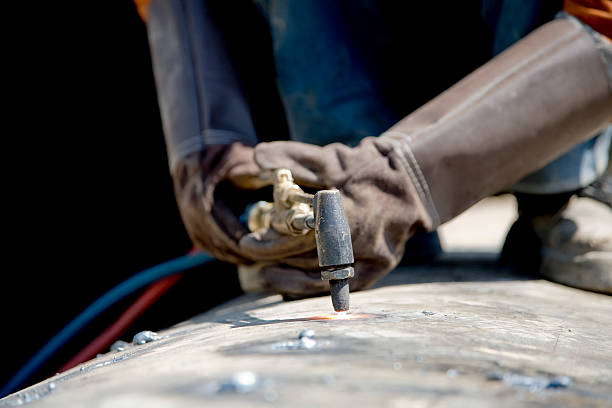
- Magnetic particle testing involves a thorough surface preparation, proper magnetization, application of magnetic particles, control of the inspection environment, and proper inspector training.
- It is crucial to maintain a clean and well-lubricated environment, maintain a stock of essential spare parts, and adhere to manufacturer guidelines for equipment maintenance.
- Proper documentation of each inspection aids in traceability and quality control. Regular inspections, calibration checks, and training on proper handling ensure accurate results and maintain the integrity of materials and components.
- By adhering to these best practices, magnetic particle inspection machine processes can consistently deliver accurate, reliable, and high-quality results.
Conclusion
Magnetic particle inspection equipment stands as a robust and versatile method for detecting defects in materials and products. From its fundamental principles to real-world applications, this guide provides a comprehensive understanding of MPI. Embrace the power of MPI to enhance the quality and reliability of your products, ensuring they meet the highest standards in safety and performance.
Key Takeaways
- MPI stands as a crucial non-destructive testing method widely utilized in diverse industries for assessing material and structural integrity.
- MPI relies on magnetism and ferrous particles to identify surface and near-surface defects, with magnetization, particle application, and defect visualization playing pivotal roles.
- Magnetic particle inspection excels at detecting various defects, including surface cracks, subsurface irregularities, weld discontinuities, and more, ensuring a thorough evaluation of material soundness.
- The method offers high sensitivity and speed, cost-effectiveness, versatility in applications across industries, and a minimal need for surface preparation.
- MPI finds widespread use in aerospace, automotive, and manufacturing, and extends to niche fields such as art restoration, offshore industries, power generation, rail transportation, and medical device manufacturing.
FAQ
No, due to the utilization of magnetics, Magnetic Particle Inspection is only applicable for ferrous materials.
Regular maintenance is recommended when utilizing a magnetic particle wet bench, UV lights and/or light meters This is typically performed at least annually or more frequently based on usage.
MPI is primarily designed for surface and near-surface defect detection. For subsurface inspection, other methods may be more suitable.
MPI is relatively environmentally friendly, but it’s essential to follow local regulations and guidelines for waste disposal.
The high sensitivity, speed, and cost-effectiveness of MPI make it a preferred choice in industries where efficient defect detection is critical.