Table of Contents
- Types of Radiography Testing
- Equipment Used in Radiography Testing
- Procedure of Radiography Testing
- Safety Measures in Radiography Testing
- Challenges in Radiography Testing
Radiography Testing involves the use of X-rays or gamma rays to examine the internal structure of an object. It is a vital technique used to detect defects such as cracks, voids, inclusions, and other discontinuities that may compromise the integrity of materials or structures.
Radiography testing procedure is widely used in industries such as aerospace, automotive, construction, and manufacturing to ensure the quality and safety of products. It plays a crucial role in identifying potential issues early on in the production process, ultimately saving time and costs associated with failures.
ALso Explore the World of Radiography : With a Focus on Film, The Backbone of Imagining Technology
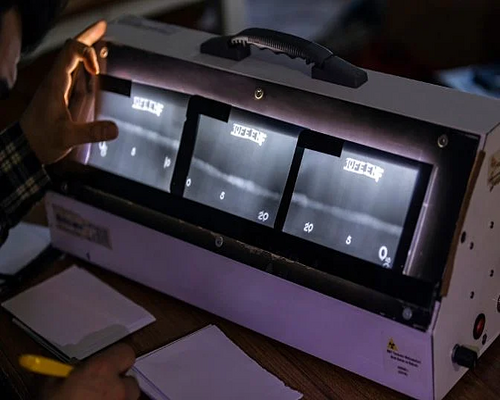
Types of Radiography Testing
There are two main types of radiography testing, film-based radiography and digital radiography. Film-based radiography involves using X-ray film to capture images, while digital radiography utilizes digital detectors to produce images that can be easily stored and analyzed. Each method has its own advantages and limitations, making it important for industries to choose the most suitable option based on their specific needs and requirements.
1. Conventional Radiography
Conventional radiography involves exposing a photographic film to X-rays or gamma rays passed through the object under inspection. The film records the radiation that the object attenuates, creating a shadow image that reveals internal features and flaws.
2. Digital Radiography
Digital radiography utilises digital detectors, such as amorphous silicon flat panels or Charge-coupled Devices (CCDs), to capture X-ray images electronically. These images can be immediately viewed and digitally manipulated for enhanced visualisation and analysis.
3. Computed Radiography
Computed Radiography employs photostimulable phosphor plates instead of film. After exposure to X-rays, the plates are scanned with a laser, releasing stored energy and producing digital images that can be processed and viewed on a computer.
Equipment Used in Radiography Testing
Equipment used in Radiography Testing includes X-ray machines, film cassettes, intensifying screens, and lead aprons. Radiographers also use digital radiography systems for faster image processing and storage. NDT radiography testing requires specialized equipment, including.
1. X-ray Machines
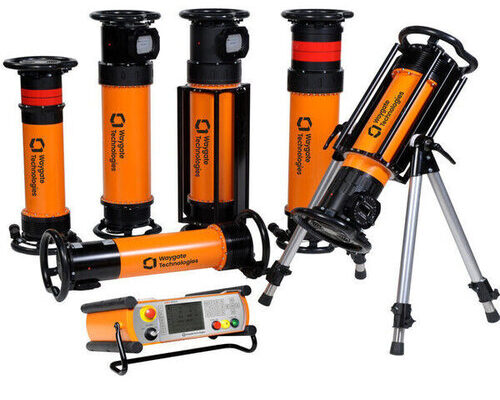
X-ray machines generate X-rays or gamma rays used for penetrating materials and producing images.
2. Film or Digital Detectors
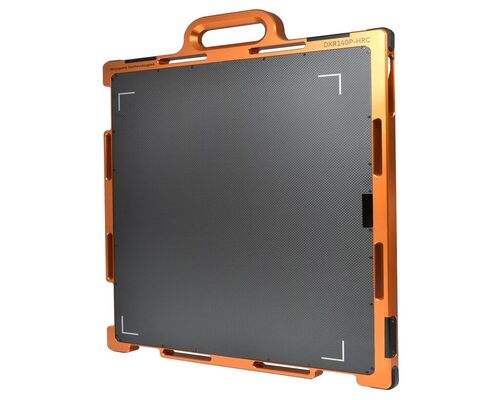
Film and digital detectors capture the radiation transmitted through the object and produce images for analysis.
3. Darkrooms
Darkrooms are used for processing and developing radiographic films in conventional radiography.
Here are the most widely used devices from NDT Products for radiography inspections.
- Waygate Technologies Digital X-ray Detectors
Elevate your radiography inspections to new heights with Waygate Technologies digital X-ray detectors. Designed for precision and efficiency, our digital detectors deliver exceptional image quality, allowing for detailed analysis and accurate defect detection. Whether you’re inspecting welds, castings, or composite materials, our digital X-ray detectors offer unparalleled performance and reliability. - Agfa Structurix NDT X-ray Film
The power of high-quality radiographic imaging with Agfa Structurix NDT X-ray film. Engineered for superior sensitivity and resolution, X-ray film produces crisp, clear images that reveal even the tiniest defects with precision. - Waygate Technologies Computed Tomography Solutions
Transform your radiographic inspections with Waygate CT Solutions. Engineered for performance and reliability, CT systems systems deliver unparalleled image quality and efficiency. Whether you’re conducting industrial inspections or medical imaging, digital X-ray solutions offer advanced features and intuitive controls for seamless operation. - Agfa Structurix X-ray Film Processor Accessories
Enhance the functionality and performance of your X-ray film processor with Agfa Structurix X-ray film processor accessories. Ensure consistent results with Agfa Structurix X-ray film processor accessories, the perfect complement to NDT Equipment.
NDT Products is known for delivering top-notch non-destructive testing solutions that exceed industry standards. With an extensive range of high-quality products and unmatched expertise, we cater to the diverse needs of clients across various sectors, from aerospace and automotive to oil and gas.
Procedure for Radiography Testing
The procedure for radiography testing procedure involves using X-rays to create images of the internal structures of an object. This Non-destructive Testing Method is commonly used in industries such as aerospace, automotive, and manufacturing to detect defects or abnormalities that may not be visible to the naked eye. It is important for radiographers to follow strict safety protocols and use x-ray procedure step by step to ensure accurate results and minimize radiation exposure. Radiography testing typically follows a systematic procedure.
1. Preparation
Preparation involves selecting the appropriate equipment, setting exposure parameters, and ensuring safety measures are in place.
2. Image Acquisition
The object under inspection is placed between the X-ray source and the detector, and an exposure is made to create a radiographic image.
3. Image Processing
Digital images are processed using specialized software to enhance contrast, brightness, and resolution for better interpretation.
4. Interpretation
Trained inspectors analyze the radiographic images to identify and evaluate any defects or anomalies present.
Reporting once the interpretation is complete, inspectors will compile a report detailing their findings and recommendations for further action. Quality control measures are implemented to ensure that the radiographic images meet industry standards and regulatory requirements.
Safety Measures in Radiography Testing
Safety is paramount in radiography testing to protect both personnel and the environment from the hazards of ionizing radiation. Measures include using shielding, monitoring radiation exposure, and employing proper handling and storage procedures for radioactive sources.
1. Utilizing Shielding
One crucial safety measure involves the implementation of shielding materials to attenuate radiation and reduce exposure levels. Lead shielding, in particular, is commonly employed to create barriers that effectively block or absorb radiation, thereby safeguarding personnel working in the vicinity of radiography equipment.
2. Monitoring Radiation Exposure
Continuous monitoring of radiation exposure is vital to assess and control the level of radiation to which individuals are exposed during radiography procedures. This is typically achieved through the use of dosimeters, which measure and record the cumulative radiation dose received by personnel over time. Regular monitoring allows for prompt identification of any potential overexposure scenarios, enabling timely intervention to mitigate risks.
3. Implementing Proper Handling Procedure
Proper handling and manipulation of radioactive sources are imperative to minimize the risk of accidental exposure or contamination. This includes adhering to established protocols for the setup, positioning, and operation of radiography equipment to ensure safe and effective testing procedures.
Challenges in Radiography Testing
Radiography testing presents various challenges that require careful consideration and innovative solutions to ensure effective and reliable inspection outcomes. Some of the key challenges in radiography testing are discussed below.
- Ensuring Consistent Image Quality and Resolution
Maintaining consistent image quality and resolution is paramount for accurate defect detection and analysis in radiography testing. Factors such as equipment performance, calibration, and technique optimization play crucial roles in achieving uniformity and clarity in radiographic images. - Minimizing Radiation Exposure to Personnel and the Environment
The safety of personnel and the environment is a primary concern in radiography testing due to the potential hazards of ionizing radiation. Minimizing radiation exposure requires adherence to strict safety protocols, including the use of shielding, monitoring devices, and exposure control measures. - Adapting Techniques for Inspecting Complex Geometries and Materials
Inspecting components with complex geometries and diverse materials poses significant challenges in radiography testing. Traditional techniques may be insufficient for adequately penetrating and imaging intricate structures or materials with varying densities and compositions.
By recognizing and addressing these challenges through continuous innovation, research, and collaboration, the field of radiography test NDT can overcome obstacles and further advance its capabilities to meet the evolving needs of various industries.
Radiography in NDTis an indispensable method for inspecting materials and structures in various industries. By employing X-rays or gamma rays to reveal internal defects without damaging the object, radiography testing ensures product quality, safety, and regulatory compliance. Despite its limitations, ongoing research and technological innovations continue to enhance the capabilities and efficiency of radiography testing, paving the way for safer and more reliable inspections in the future. Visit NDT Products today to explore a range of non-destructive testing solutions and elevate inspection capabilities to new heights.