Table of Content
- What is Remote Visual Inspection?
- Key Technologies in Remote Visual Inspection
- Applications of Remote Visual Inspection
- Benefits of Using Remote Visual Inspection
- Challenges in Remote Visual Inspection
- Future of Remote Visual Inspection
- Conclusion
Remote Visual Inspection (RVI) is a non-destructive testing method that allows for the inspection of hard-to-reach areas using cameras and other visual equipment. This technology is commonly used in industries such as aerospace, oil and gas, and power generation to assess the condition of equipment and structures without causing damage.
RVI allows for the examination of inaccessible or hazardous areas without direct human intervention. By providing real-time visuals, RVI helps identify potential issues early on and prevent costly downtime or accidents. This method is essential for maintaining the integrity and safety of critical infrastructure.
What is Remote Visual Inspection?
Remote Visual Inspection, or RVI, is a Non-destructive Testing Method that utilizes various technologies to remotely inspect and assess the condition of equipment and structures. This method enables inspectors to view and record internal surfaces and components without needing to disassemble the object being inspected.
RVI typically uses tools such as borescopes, fiberscopes, videoscopes, and robotic crawlers equipped with cameras. These devices can be inserted into small openings, pipes, or confined spaces to provide real-time visual feedback and high-resolution imagery. The images and videos captured can then be analyzed to identify defects, corrosion, cracks, misalignments, and other potential issues.
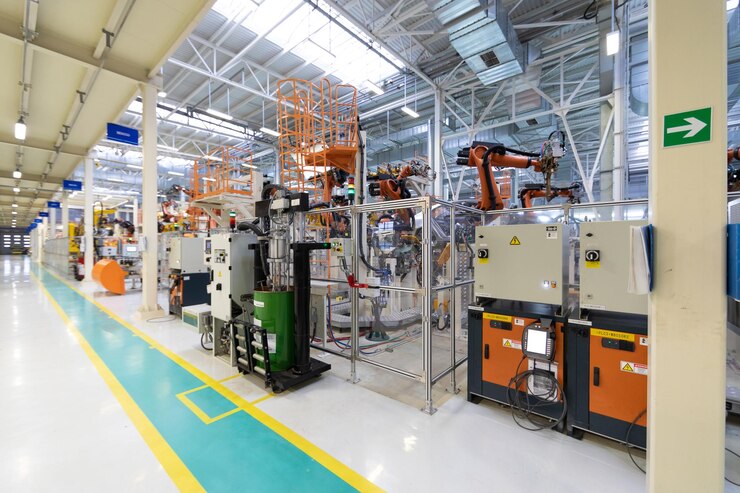
There are many advantages of remote visual inspection. The key advantages of RVI are discussed below.
- Safety: Reduces the need for personnel to enter dangerous or hard-to-reach areas:
- Cost-effectiveness: Minimizes downtime and avoids the need for extensive disassembly and reassembly.
- Accuracy: Provides detailed visual information that can aid in precise diagnostics and decision-making.
- Efficiency: Speeds up the inspection process and allows for quicker identification of issues.
RVI is widely used in industries such as aerospace, oil and gas, power generation, manufacturing, and infrastructure maintenance. By enabling thorough inspections without invasive procedures, RVI helps maintain the integrity and performance of critical systems while ensuring safety and reliability.
Key Technologies in Remote Visual Inspection
Key technologies commonly used in RVI include borescopes, videoscopes, and robotic crawlers. These tools allow inspectors to access hard-to-reach areas and provide high-quality images for accurate assessment.
1. Video Borescopes
Video Borescopes are perhaps the most widely used RVI tools. They consist of a flexible tube with a camera at the end, allowing inspectors to navigate through tight spaces and capture high-quality video footage of the area being inspected.
2. Fiberscopes
Fiberscopes use fibre-optic cables to transmit images from the inspection site to a viewing device. While they offer less image quality compared to video borescopes, fiberscopes are highly flexible and can reach areas that are otherwise inaccessible.
3. Robotic Crawlers
Robotic Crawlers are used in environments that are too dangerous or challenging for human inspectors. Equipped with cameras and other sensors, these remotely operated robots can traverse pipelines, ducts, and other confined spaces to provide detailed inspection data.
4. Drones
Drones are increasingly being used for RVI, particularly in industries like power generation and oil and gas. Equipped with high-resolution cameras and sensors, drones can inspect large structures, such as wind turbines and oil rigs, without the need for scaffolding or ladders.
The Sensor Networks HD PTZx Industrial Camera System, designed for those who demand supreme clarity and meticulous detail in their inspections. This avant-garde camera system boasts high-definition visuals and an expansive zoom capability, enabling operators to scrutinize the minute components of industrial structures.
Mentor Visual iQ Plus HD VideoProbe uses high-definition imaging with intuitive operation, offering an extraordinary tool for non-destructive testing professionals. The iQ Plus is engineered into the most inaccessible areas, providing crystal-clear imagery and advanced analytical capabilities.
The CRxVision system offers better image resolution and processing capabilities, empowering users to detect and analyze imperfections with heightened accuracy. It simplifies the radiographic process, delivering swift, reliable results while minimizing downtime. With CRxVision, elevate your inspection processes to new heights of efficiency and precision, ensuring that no detail goes unnoticed.
Applications of Remote Visual Inspection
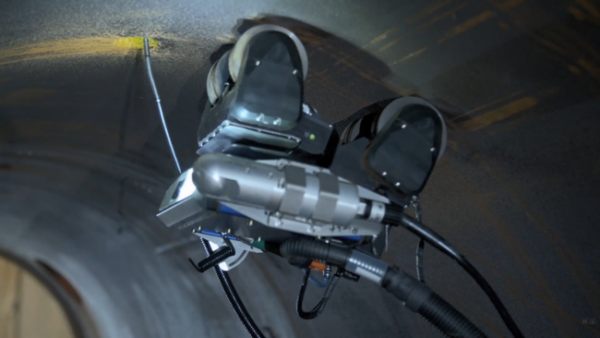
Applications of RVI include inspection of hard-to-reach areas in industrial settings, such as pipelines and machinery, as well as search and rescue operations in hazardous environments. RVI technology can also be used for medical procedures, such as minimally invasive surgeries and diagnostic imaging.
1. Industrial Applications
In manufacturing plants, RVI is used to inspect machinery, welds, and other critical components. This helps in early detection of wear and tear, preventing costly breakdowns.
2. Aerospace Industry
The aerospace industry relies heavily on RVI for inspecting engines, airframes, and other components. Ensuring the integrity of these parts is vital for safety and performance.
3. Power Generation
Power plants, especially nuclear facilities, use RVI to inspect turbines, reactors, and other critical infrastructure. This helps in maintaining operational efficiency and safety standards.
4. Oil and Gas Industry
In the oil and gas sector, RVI is used to inspect pipelines, storage tanks, and offshore platforms. This is crucial for preventing leaks and ensuring environmental compliance.
5. Construction and Civil Engineering
RVI is employed in the construction industry to inspect bridges, tunnels, and other structures. It helps in assessing structural integrity and identifying potential issues before they become serious problems.
Aslo Read: Visual Inspection of Part Defects: Methods, Challenges, and Opportunities
Benefits of Using Remote Visual Inspection
Benefits of using remote visual inspection include increased safety for workers by reducing the need for physical presence in hazardous environments, as well as improved efficiency and accuracy in identifying defects or issues in hard-to-reach areas. Additionally, remote visual inspection can lead to cost savings by minimizing downtime for equipment maintenance and repairs. A few benefits are discussed below in detail:
1. Safety
One of the biggest advantages of RVI is enhanced safety. Inspectors can assess hazardous or hard-to-reach areas without exposing themselves to danger.
2. Cost-Effectiveness
By reducing the need for disassembly and minimizing downtime, RVI significantly cuts inspection costs. This is particularly beneficial in industries where downtime can be extremely expensive.
3. Efficiency
RVI allows for quicker inspections compared to traditional methods. This means less downtime and faster identification of issues, leading to more efficient maintenance schedules.
4. Detailed Reporting
Modern RVI tools can capture high-resolution images and videos, providing detailed documentation of inspections. This data can be used for further analysis and reporting, aiding in better decision-making.
Challenges in Remote Visual Inspection
Challenges in RVI include the need for skilled operators and potential limitations in certain environments. Additionally, ensuring proper calibration and maintenance of RVI Equipment is crucial to obtaining accurate results.
1. Technological Limitations
Despite significant advancements, RVI technology still has limitations. For instance, image resolution might not be sufficient for detecting very fine defects, and navigating extremely complex structures can be challenging.
2. Operator Training
Effective RVI requires skilled operators who can correctly interpret the data gathered. Ensuring that inspectors are properly trained is crucial for accurate assessments.
3. Environmental Factors
Conditions such as poor lighting, extreme temperatures, and corrosive environments can affect the performance of RVI equipment. Adapting to these challenges requires robust and reliable technology.
NDT Products is known for delivering top-notch NDT solutions that exceed industry standards. With an extensive range of high-quality products and unmatched expertise, we cater to the diverse needs of clients across various sectors, from aerospace and automotive to oil and gas.
Whether you’re seeking Ultrasonic Testing Equipment, magnetic particle inspection tools, or radiographic testing accessories, we’ve got you covered with precision-engineered solutions designed to enhance efficiency and ensure utmost reliability in every inspection task.
Our commitment to innovation and customer satisfaction sets us apart as a trusted leader in the NDT industry. Trust NDT Products for all your non-destructive testing needs, and experience the difference in quality and performance.
Future of Remote Visual Inspection
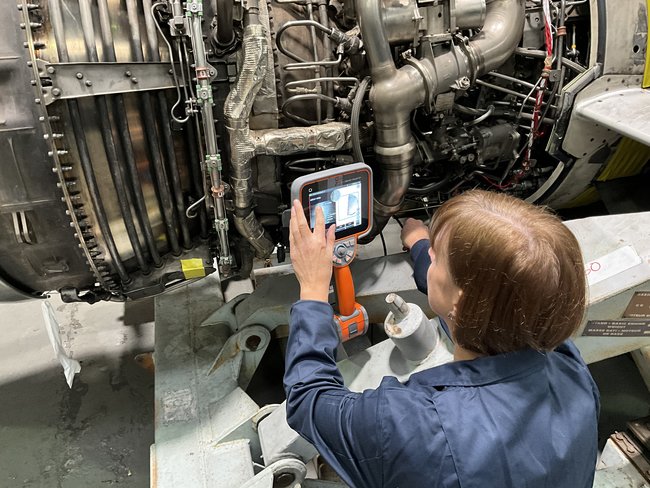
Remote visual inspection lies in the development of advanced robotics and artificial intelligence technologies. These innovations will enable more efficient and accurate inspections in hard-to-reach or hazardous environments, ultimately improving safety and productivity in various industries.
1. Advances in Technology
The future of RVI looks promising with continuous advancements in technology. Improvements in camera resolution, battery life, and wireless communication are expected to enhance the capabilities of RVI Tools.
2. Integration with AI
Artificial Intelligence (AI) is set to revolutionize RVI by enabling automated defect detection and analysis. AI algorithms can quickly analyze large volumes of inspection data, identifying issues that might be missed by human inspectors.
3. Enhanced Data Analytics
Advanced data analytics will allow for better trend analysis and predictive maintenance. By analyzing historical inspection data, AI can help predict when and where issues are likely to occur, enabling proactive maintenance strategies.
Conclusion
Remote visual inspection offers safer, more efficient, and cost-effective alternative to traditional inspection methods. As technology continues to evolve, the capabilities and applications of RVI are set to expand even further, making it an indispensable tool for maintaining the integrity and safety of critical infrastructure.
With a commitment to innovation and customer satisfaction, NDT Products stands at the forefront of the NDT industry, offering not just products, but the best solutions tailored to meet the unique requirements of each client. Trust NDT Products for all your non-destructive testing needs and experience unparalleled performance, durability, and peace of mind with every inspection. With a team of experts dedicated to continuous improvement and customer support, NDT Products ensures that you receive top-notch service and reliable products every time. Choose NDT Products for all your non-destructive testing needs and discover the difference that quality and innovation can make in your operations.