Table of Content
- How Ultrasonic Transducers Work?
- Types of Ultrasonic Transducers
- Ultrasonic Transducer Probes
- Ultrasonic Transducer Materials
- Design and Specifications
- Applications of Ultrasonic Transducers
- Ultrasonic Testing for Flaw Detection
- Benefits of Ultrasonic Testing
- Limitations of Ultrasonic Testing
- How to Choose the Best Ultrasonic Transducer
- Buying Guide
- Maintenance and Care
- Future of Ultrasonic Transducers
- Conclusion
Ultrasonic transducers devices play a critical role in various fields, from industrial testing to medical imaging. These devices are used for different purposes, such as detecting flaws in materials or creating detailed images.
How Ultrasonic Transducers Work?
The fundamental principle behind ultrasonic transducers is the conversion of electrical energy into mechanical vibrations (ultrasonic waves) and vice versa. This is primarily achieved using materials that exhibit piezoelectric properties. When an electrical signal is applied to these materials, they deform and create mechanical vibrations at ultrasonic frequencies.
Types of Ultrasonic Transducers
Ultrasonic ransducers are available in various types. Each Type of Ultrasonic Transducer has specific advantages and limitations, depending on the application requirements.
1. Piezoelectric Transducers
Piezoelectric transducers are the most common types of ultrasonic transducers. They use piezoelectric materials like quartz or ceramics to generate and receive ultrasonic waves.
2. Magnetostrictive Transducers
Magnetostrictive transducers use magnetostrictive materials, which change shape in response to magnetic fields. They are often used in high-power applications due to their durability.
Ultrasonic Transducer Probes
Ultrasonic transducer probes are used in a variety of applications, including imaging, distance sensing, and non-destructive testing. Various types of ultrasonic transducer probes emit high-frequency sound waves and then detect the echoes that bounce back, allowing for precise measurements and imaging.
1. Contact Probes
Contact probes are used directly on the surface of the object being tested. They are ideal for detecting flaws in solid materials.
2. Immersion Probes
Used in a liquid medium, immersion probes are excellent for applications requiring detailed imaging.
3. Angle Beam Probes
Angle beam probes introduce ultrasonic waves at an angle, making them suitable for inspecting welded joints and other complex structures.
Ultrasonic Transducer Materials
Ultrasonic transducer materials play a crucial role in the performance and durability of ultrasonic devices. Common materials used include piezoelectric ceramics, polymers, and composites.
1. Piezoelectric Materials
Common materials include lead zirconate titanate (PZT) and quartz. These materials are chosen for their high sensitivity and efficiency in converting electrical signals to ultrasonic waves.
2. Backing Materials
Materials like tungsten or epoxy are used to absorb excess vibrations and enhance the transducer’s performance.
3. Matching Layers
A layer of material with intermediate acoustic impedance is used to improve the transmission of ultrasonic energy into the test medium.
Design and Specifications
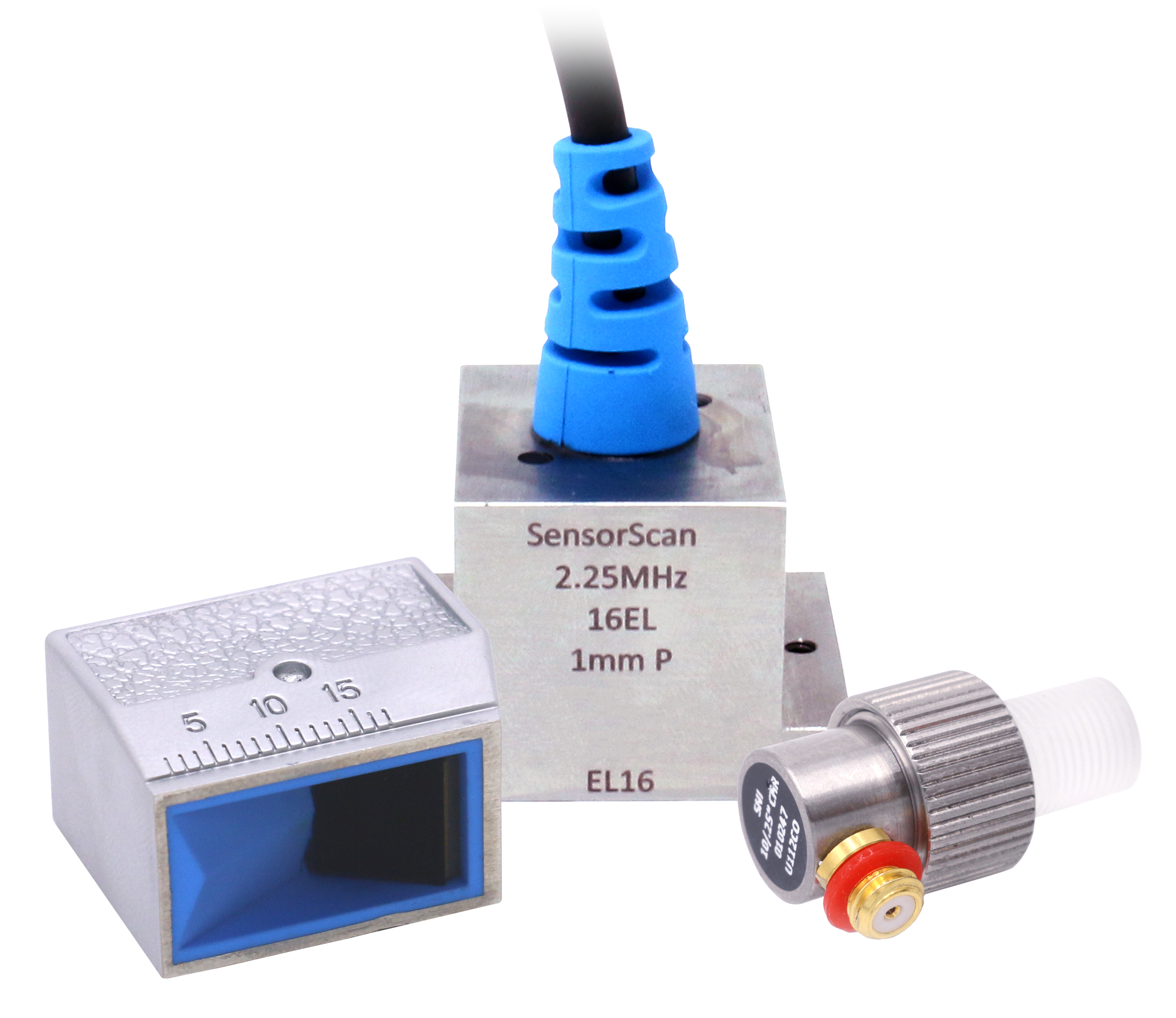
Design and specifications play a crucial role in the success of any product. For ultrasonic transducer buy the functionality, features,ultrasonic transducer design, and requirements are necessary. These elements must be carefully considered to ensure the final product meets user needs and expectations.
1. Frequency Range
Ultrasonic transducers can operate at various frequencies, typically ranging from 1 MHz to 20 MHz. The frequency affects the resolution and penetration depth of the ultrasonic waves.
2. Beam Profile
The shape and size of the ultrasonic beam are crucial for accurate detection and imaging. Different applications may require focused or divergent beams.
3. Sensitivity
The sensitivity of a transducer determines its ability to detect small flaws or produce detailed images. High sensitivity is essential for applications like medical imaging.
Applications of Ultrasonic Transducers
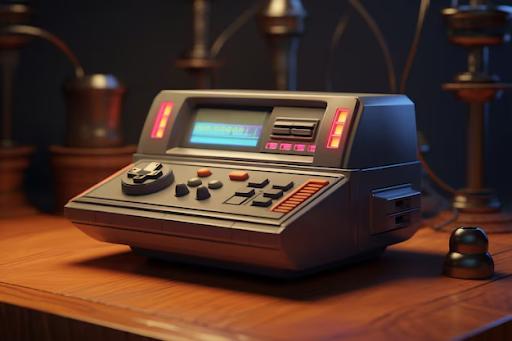
Ultrasonic transducer applications are very diverse across various industries. From the various ultrasonic transducer types, the ideal one is chosen according to the necessities.
1. Industrial Testing
In industries, these transducers are used for non-destructive testing to detect flaws, measure thickness, and inspect materials without causing damage.
2. Underwater Sonar
In marine applications, ultrasonic transducers are used in sonar systems to map the seabed, detect underwater objects, and aid in navigation.
3. Medical Imaging
Ultrasonic transducers are widely used in medical imaging techniques like ultrasound to create images of internal body structures, aiding in diagnostics and monitoring.
Ultrasonic Testing for Flaw Detection
Various techniques are used for Ultrasonic Testing for Flaw Detection, like pulse-echo, through-transmission, and phased array, which are used in ultrasonic testing to detect internal flaws in materials.
1. Pulse-Echo Technique
The pulse-echo technique is one of the most commonly used methods in ultrasonic testing. It works by sending a short ultrasonic pulse into the material. When the pulse encounters a flaw or boundary within the material, it reflects back to the transducer. The time it takes for the echo to return helps determine the location and size of the flaw.
2. Through-Transmission Technique
In the through-transmission technique, two transducers are used, one to send the ultrasonic pulse and another to receive it on the opposite side of the material. This method is particularly effective for detecting flaws that may not be detectable by the pulse-echo method.
3. Phased Array Technique
The phased array technique involves using multiple transducer elements in a single probe. By electronically controlling the timing of each element, the sound beam can be steered and focused at different angles and depths.
Benefits of Ultrasonic Testing
Ultrasonic testing offers several advantages that make it a preferred choice for flaw detection. These benefits include the ability to detect internal and surface defects in materials, as well as the capability to provide accurate measurements of material thickness.
- High Degree of Accuracy: UT can detect very small flaws with precise measurements.
- Depth Penetration Capabilities: Sound waves can penetrate deep into materials, making it suitable for thick structures.
- Non-Destructive Nature: The material being tested remains intact, allowing for continuous use without damage.
- Versatility: UT can be applied to a wide range of materials, including metals, plastics, and composites.
Limitations of Ultrasonic Testing
- Despite its many benefits, ultrasonic testing has some limitations. A few common obstacles are discussed here.
- Requirement for Skilled Operators: Proper training and experience are essential to interpreting results accurately.
- Material Properties: Certain materials, such as coarse-grained metals, can scatter sound waves, making it difficult to detect flaws.
- Equipment Cost and Maintenance: High-quality UT equipment can be expensive and requires regular maintenance to ensure optimal performance.
How to Choose the Best Ultrasonic Transducer
For choosing the best ultrasonic transducer, consider factors like frequency, sensitivity, application requirements, and the environment in which it will be used. When selecting an ultrasonic transducer, several factors should be considered.
- Frequency: Higher frequencies provide better resolution but lower penetration, while lower frequencies penetrate deeper but with less detail.
- Sensitivity: Choose a transducer with appropriate sensitivity for the specific application.
- Application Requirements: Consider the material type, thickness, and desired inspection depth.
- Environmental Factors: Ensure the transducer can withstand the operating environment, including temperature, humidity, and potential contaminants.
NDT Products is known for delivering top-notch non-destructive testing solutions that exceed industry standards. With an extensive range of high-quality products and unmatched expertise, we cater to the diverse needs of clients across various sectors, from aerospace and automotive to oil and gas.
Buying Guide
Ultrasonic transducers can be purchased from specialized suppliers, online marketplaces, and ultrasonic transducer manufacturers.
- Specialized Suppliers: Companies that specialize in non-destructive testing equipment.
- Online Marketplaces: Websites like Amazon and eBay offer a variety of options.
- Directly from Manufacturers: Purchasing directly ensures access to the latest products and technologies.
The cost of ultrasonic transducers varies based on their type, specifications, and application. Ultrasonic Transducer specifications include frequency range, power output, and transducer material.Investing in a high-quality transducer may have higher upfront costs but can save money in the long run through durability and accuracy.
Sensor Networks, Inc. is a Pennsylvania-based technology company specializing in designing and manufacturing industrial ultrasonic transducers and tooling for demanding in-situ test and inspection applications.
Waygate offers a range of Krautkramer Ultrasonic Contact Transducers and probes, such as multiple straight beam single elements, straight beam dual elements, and angle beam options, renowned for their durability, ease of use, and accuracy.
Maintenance and Care
When it comes to the maintenance and care of ultrasonic transducers, it is important to regularly check for any signs of wear or damage to the components. Additionally, ensuring that the ultrasonic transducer frequency is properly calibrated and functioning optimally will help prolong its lifespan and maintain its effectiveness.
1. Cleaning and Storage
Regular cleaning and proper storage are crucial for maintaining the performance and longevity of ultrasonic transducers. Use appropriate cleaning solutions and store transducers in a dry, temperature-controlled environment to prevent damage.
2. Calibration
Periodic calibration is essential to ensure the accuracy and reliability of ultrasonic transducers, especially in critical applications. Employing certified equipment and qualified personnel should be the standard for calibration.
Future of Ultrasonic Transducers
The future of ultrasonic transducers can be seen with a lot of advancements in technology that continue to improve their performance and capabilities. With ongoing research and development, we can expect to see even more innovative applications for ultrasonic transducers in various industries, such as healthcare, manufacturing, and robotics.
1. Technological Advancements
Emerging technologies are continuously enhancing the capabilities of ultrasonic transducers. Improvements in materials, higher frequencies, and advanced imaging techniques are making UT more accurate and efficient.
2. Emerging Applications
- Ultrasonic transducers are finding new applications in various fields:
- Biotechnology: Used for imaging and diagnostic purposes.
- Environmental Monitoring: Helps in detecting pollutants and assessing environmental conditions.
- Advanced Manufacturing: Enables precise quality control and flaw detection in high-tech industries.
Conclusion
Ultrasonic transducers play a crucial role in improving efficiency and accuracy in fields such as non-destructive testing. As technology continues to evolve, we can expect to see even more development in ultrasonic transducer capabilities and applications. Check out NDT Products today to explore a range of non-destructive testing solutions and elevate inspection to new heights.