Table of Content
- What is Visual Inspection?
- Types of Visual Inspection Methods
- Technologies Used in Visual Inspection
- Common Part Defects Detected by Visual Inspection
- Challenges in Visual Inspection
- Overcoming Challenges in Visual Inspection
- Opportunities for Improvement in Visual Inspection
- Future Trends in Visual Inspection
- Key Takeaways
Visual inspection is the cornerstone of quality assurance in manufacturing. It involves scrutinising products to identify defects, ensuring that only high-quality items reach consumers. Visual inspection of part defects is crucial for maintaining product integrity, customer satisfaction, and regulatory compliance.
By detecting defects early on, visual inspection helps prevent costly recalls and damage to a company’s reputation. Implementing advanced technologies like machine vision systems can further enhance the accuracy and efficiency of this critical quality control process.
What is Visual Inspection?
Visual inspection involves examining products or parts to identify defects. Human inspectors can perform it manually or automatically using technology. The primary purpose is to ensure that the items meet specified quality standards and are free from defects that could impair functionality or safety.
Visual inspection is an essential quality control method used in various industries, such as manufacturing, electronics, and automotive. It helps companies maintain high-quality standards and prevent defective products from reaching the market.
Types of Visual Inspection Methods
Types of visual inspection methods include direct visual inspection, Remote Visual Inspection, and automated visual inspection. Direct visual inspection involves physically examining an object or surface with the naked eye or with the help of magnifying tools.
Remote visual inspection uses cameras or other devices to inspect objects in hard-to-reach or hazardous areas. Automated visual inspection involves using computer algorithms and machine vision systems to analyze images and detect defects in products during the manufacturing process. Let’s discuss it in detail.
1. Manual Visual Inspection
Trained personnel visually evaluate each part during a manual visual inspection. This method relies on the inspector’s ability to identify defects based on their knowledge and experience.
2. Automated Visual Inspection
Automated visual inspection uses machines and software to detect defects. These systems often employ cameras, sensors, and artificial intelligence to analyze parts with high precision and consistency.
Comparison Between Manual and Automated Methods
Manual inspection offers flexibility and the ability to detect a wide range of defects. However, it is prone to human error and can be time-consuming. Despite its programming and initial setup costs, automated inspection produces faster and more reliable results.
Technologies Used in Visual Inspection
Technologies used in visual inspection include machine learning algorithms, computer vision, and artificial intelligence to analyze images and detect defects in products. These technologies have greatly improved the accuracy and efficiency of quality control processes in manufacturing industries.
1. Optical Cameras
Optical cameras are commonly used in automated visual inspection systems. They capture high-resolution images of parts for detailed analysis.
2. Microscopes
Microscopes are essential for inspecting small or intricate parts that require magnification to identify defects.
3. Laser Scanners
Laser scanners provide precise measurements of part dimensions and can detect surface defects that may not be visible to the naked eye.
4. Borescope
Borescope inspection involves using a specialized optical tool to view the interior of hard-to-reach spaces. The primary purpose is to detect defects, ensure compliance with quality standards, and maintain the integrity of components.
The Mentor Visual iQ+ HD VideoProbe is revolutionizing remote visual inspections with artificial intelligence and cloud-based digital tools. It features updated analytical models, gas power-assist, and Aiir Innovation, Edge Hot, and Edge Cold. Blade Counter 2.0 is quicker, robust, and more intuitive, automatically tracking gas turbine blades in real time.
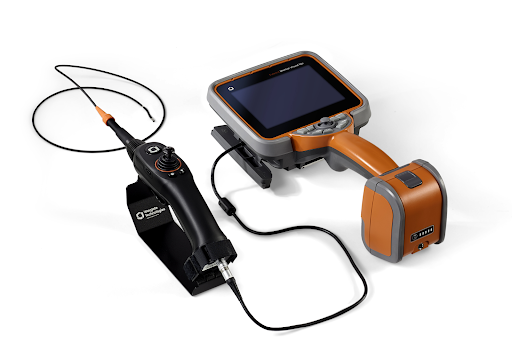
NDT Products is known for delivering top-notch non-destructive testing solutions that exceed industry standards. With an extensive range of high-quality products and unmatched expertise, we cater to the diverse needs of clients across various sectors, from aerospace and automotive to oil and gas.
Common Part Defects Detected by Visual Inspection
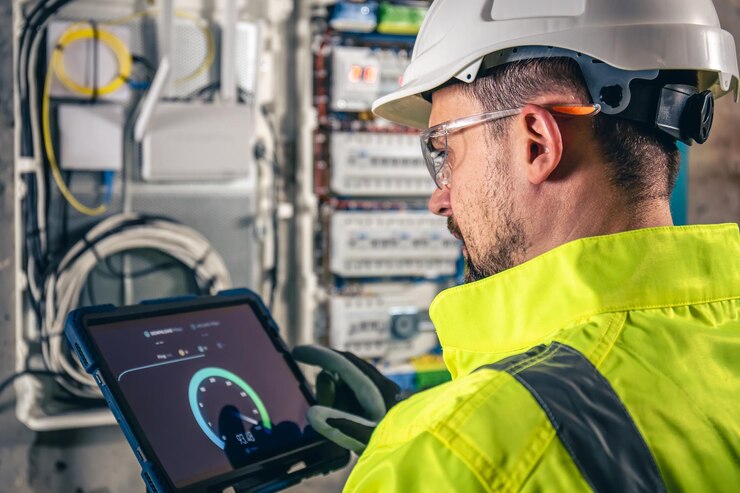
Common part defects detected by visual inspection include scratches, dents, cracks, and misalignments. These defects can impact the functionality and safety of the final product if they are not detected and corrected during the manufacturing process.
1. Surface Defects
Surface defects include scratches, dents, and discolorations that affect the part’s appearance and potentially its performance.
2. Dimensional Defects
Dimensional defects refer to variations from the specified measurements, which can affect the part’s fit and function.
3. Structural Defects
Structural defects, such as cracks or voids, compromise the part’s integrity and can lead to failure under stress.
Challenges in Visual Inspection
Challenges in visual inspection include identifying defects in complex or hard-to-reach areas, as well as distinguishing between acceptable variations and actual defects. Implementing advanced imaging technologies and automated inspection systems can help overcome these challenges and improve the efficiency and accuracy of visual inspections.
1. Human Error in Manual Inspection
Human error is a significant challenge in manual inspection. Factors like fatigue, distraction, and inconsistent judgement can lead to missed defects.
2. Limitations of Automated Systems
Automated systems, while precise, can miss defects that were not anticipated during programming. They also require significant investment and maintenance.
3. Environmental Factors
Lighting, temperature, and cleanliness of the inspection environment can impact the accuracy of both manual and automated inspections.
Overcoming Challenges in Visual Inspection
Overcoming challenges in visual inspection requires a combination of well-trained personnel, regularly updated automated systems, and optimal environmental conditions. By addressing these factors, organizations can improve the accuracy and efficiency of their inspection processes.
1. Enhancing Human Inspection Skills
Investing in training programs can improve the skills and accuracy of human inspectors. Regular refresher courses and certifications ensure inspectors stay current with best practices.
2. Advances in Machine Learning and AI
Machine learning and AI technologies enhance automated inspection systems by enabling them to learn from data and improve over time.
3. Environmental Control Measures
Maintaining optimal inspection conditions through proper lighting, temperature control, and cleanliness can enhance the accuracy of visual inspections.
Opportunities for Improvement in Visual Inspection
Opportunities for improvement in visual inspection include implementing automated inspection systems to reduce human error and increase efficiency. Additionally, incorporating machine learning algorithms can help identify defects more accurately and quickly, leading to higher quality control standards.
1. Integration with Other Quality Control Methods
Combining visual inspection with other quality control methods, such as ultrasonic testing or X-ray inspection, can provide a more comprehensive assessment of part quality.
2. Real-time Data Analysis
Real-time data analysis enables immediate feedback and corrective actions, reducing the chances of defective parts progressing through the production line.
3. Predictive Maintenance
Visual inspection data can be used for predictive maintenance, identifying potential failures before they occur, and minimizing downtime.
Future Trends in Visual Inspection
Future trends in visual inspection methods include the integration of artificial intelligence and machine learning algorithms to enhance defect detection and classification. This technology will enable faster and more accurate inspections, ultimately improving product quality and reducing production costs.
Additionally, advancements in image analysis software may also play a significant role in automating visual inspection processes, further increasing efficiency and consistency in manufacturing operations.
AI and Machine Learning Integration
AI and machine learning will continue to enhance the capabilities of visual inspection systems, making them smarter and more adaptable.
Improved Sensor Technologies
Advancements in sensor technologies will allow for more precise detection of defects, even in complex and small parts.
Remote Inspection Capabilities
Drones and internet-connected devices will make it possible to conduct remote visual inspection in risky or challenging environments.
With a commitment to innovation and customer satisfaction, NDT Products stands at the forefront of the NDT industry, offering not just products, but the best solutions tailored to meet the unique requirements of each client. Trust NDT Products for all your non-destructive testing needs and experience unparalleled performance, durability, and peace of mind with every inspection.
Key Takeaways
Visual inspection plays a crucial role in ensuring product quality across various industries.
From manual methods to sophisticated automated systems, this process has evolved significantly.
Despite challenges, technological advances offer promising opportunities for enhancing defect detection and improving overall manufacturing quality.
The future of visual inspection looks bright, with AI, predictive maintenance, and human-machine collaboration set to drive further innovations.